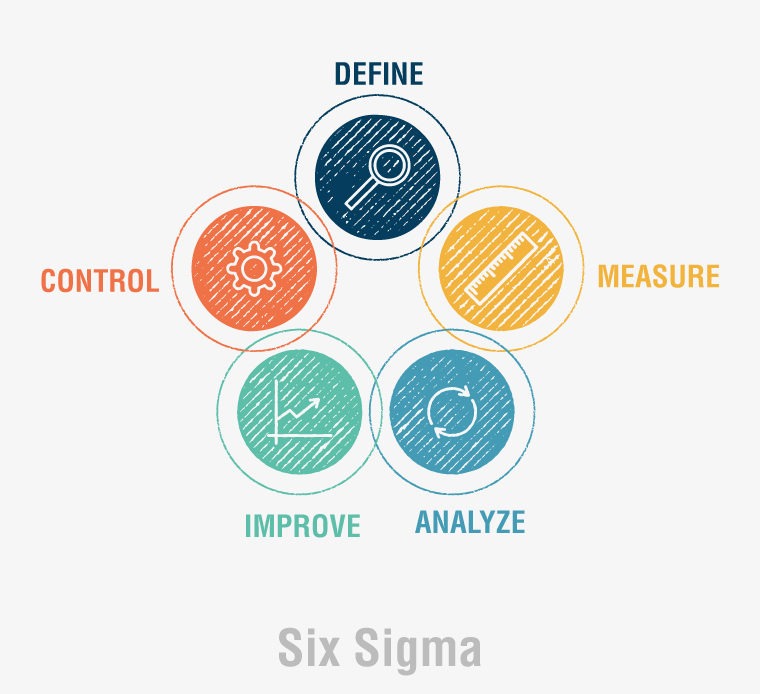
What is LEAN SIX SIGMA?
Lean Six Sigma is a proven process improvement framework that results in high level of competence in business process improvement techniques and more importantly, to make a real difference to your company’s performance, in other way it improves processing time and increases quality at a lower cost. This framework maximizes value by eliminating waste and improving process capabilities and focuses on change management and sustainability also experiences less waste at catalytic speed. It closely works with ISO 9001 requirement for Practical and process approach. On ground, it is the combination of Lean Management system and Six Sigma. In current trend a few companies are get benefited by adopting this methodology. Qualitcert creates a strategic atmosphere, where helps the organization to be more focus on the highest value activities, overcome obstacles, organize efficiently, align your business processes with your strategy and ensure that all functional elements are working in unison.
Up Your Business -Talk to our experts learn more about LEAN SIX SIGMA
ISO 9001:2015
Why LEAN SIX SIGMA?
We have global expertise in multiple disciplines critical to Lean Six Sigma. Our approach focuses on the areas of greatest value, for example:-
● Lower operational costs
● Lower indirect costs
● Reduced administration
● Greater responsiveness
● Lower material waste and rework
● Better use of time and resources
● Lower internal process and supply chain risk
● Faster time to market
● Enhanced brand reputation
● Greater engagement by workforce
● Enhanced skillset available to the organization
Our SME’s know how to navigate effectively at all levels of an organization and bring about the partnerships, synergies and changes that are required for Lean Six Sigma programme to be successful.
Qualitcert follows both traditional and innovative Lean Six sigma framework in out consulting clients. We use DMAIC methodology for problem solving, and its start with identifying the area in each business process and customize every process to meet its specific needs and maximize performance improvement. During Define Phase, we will work closely with your team to help developing a customized plan tailored to your specific situation and your organizational culture. We will determine the best approach to achieve your goals and objectives. Through measure phase, we will develop data collection plan to measure the current performance of the process to be improved. During the analysis phase, the process to establish the main root cause of poor performance and conduct an efficiency analysis to determine the underlying process issues. In improve phase, Guide the Management and process owners through testing and studying potential solutions to establish a robust improved process for achieving the objectives. During this last phase, the improved process by establishing a standardized process capable of being operated and continually improved to maintain performance over time.